Tungsten Carbide Rolls
Tungsten carbide rolls by Hyperion Materials & Technologies are designed to improve the performance and durability of rolling mills by providing superior wear resistance, thermal stability, and dimensional accuracy. Made from a blend of high-performance materials, including cobalt, nickel, and tungsten carbide, they are engineered to withstand the harsh demands of rolling mills and steel production.
Hyperion tungsten carbide rolls are well-suited for a better production economy in the rolling mill and offer a number of advantages over traditional cast iron and steel rolls, including:
• Increased productivity
• Reduced maintenance costs
• Improved product quality
• Longer roll and passform life
Product Groups
Hyperion Code: CIC-Integral
Description: Fully integrated roll. A tungsten carbide layer bonded to a cast iron arbor without locking or clamping mechanisms.
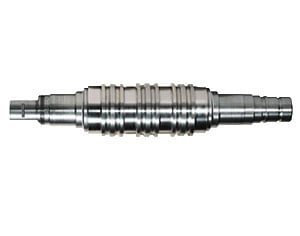
Hyperion Code: CIC-Combi
Description: Tungsten carbide layer bonded to a cast iron ring, allowing exchangeable carbide rings to be mounted into a cast iron or steel arbor.
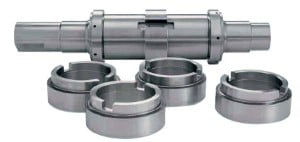
Hyperion Code: Talus Clamping System
Grades: See grade data
Description: Hydraulic or mechanical clamping systems that can be tailored to any rolling mill operation to facilitate ring exchange.
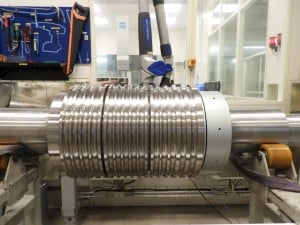
Hyperion Code: CIC-Integral
Description: Fully integrated roll. A tungsten carbide layer bonded to a cast iron arbor without locking or clamping mechanisms.
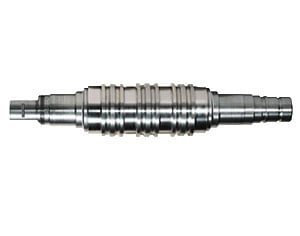
Hyperion Code: CIC-Combi
Description: Tungsten carbide layer bonded to a cast iron ring, allowing exchangeable carbide rings to be mounted into a cast iron or steel arbor.
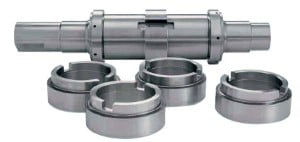
Hyperion Code: Talus Clamping System
Grades: See grade data
Description: Hydraulic or mechanical clamping systems that can be tailored to any rolling mill operation to facilitate ring exchange.
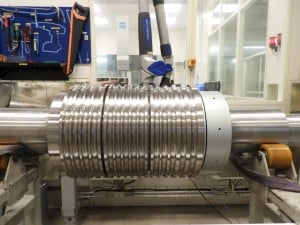
Cast-in-Carbide (CIC™) Rolls
Cast-in-carbide (CIC™) rolls from Hyperion Materials & Technologies are the ultimate in durability and performance for rolling mills. Made with a tungsten carbide layer bonded to a cast iron ring, these rolls are incredibly hard and wear-resistant, making them ideal for high-volume production. CIC™ rolls also have excellent thermal conductivity, which helps to dissipate heat and prevent the rolls from overheating. As a result, CIC™ rolls from Hyperion offer a longer service life, lower maintenance costs, and improved product quality.
In addition to their durability and performance, CIC™ rolls are also very versatile. Hyperion can help design CIC™ rolls in a variety of sizes and shapes to meet the specific needs of your rolling mill.
CIC™ Integral
CIC™ Integral rolls are optimized for the early and intermediate stands in the rolling mill. CIC™ Integral rolls best suited for the highest rolling torque and force and low rolling speeds, even below 1 m/sec. The cast iron arbor and the cemented tungsten carbide rings are cast and machined in one solid piece, with no keys, no keyways, and no locking nut. This allows higher torque transmission than that of conventional combi rolls. The absence of a locking device also allows for more passforms for productive hot rolling.
CIC™ Combi
The CIC™ Combi roll by Hyperion consists of CIC™ rings secured to a cast iron or steel arbor with locking nuts, keys, drive pins, bolts, and spacers. Because the CIC™ rings are exchangeable, CIC™ Combi Rolls allow for a versatile range of design options that can be tailored to each application.
Talus™ Rolls
Talus™ system rolls are composite rolls assembled with tungsten carbide rings that can use either a mechanical or hydraulic clamping system. The Talus™ system expands our complete set of composite rolls solutions, allowing us the flexibility to offer a tailor-made roll for any rolling mill application.
FAQs about Carbide Rolls
Tungsten carbide rolls can be used in the intermediate finishing sections of rolling mills.
Hyperion can produce tungsten carbide rolls with outer diameters of up to 550 millimeters.
To convert from cast iron or steel rolls to tungsten carbide rolls, Hyperion carbide rolls product speciailists will partner with rolling mills to revise roll cooling, machining, and handling capabilities. Most rolling mills can easily adapt from cast iron to tungsten carbide.
Hyperion tungsten carbide rolls have a longer lifespan of up to 20 times longer than that of cast iron rolls due to their higher wear resistance. This results in reduced stoppage time for the rolling mill along with higher productivity and lower operational costs
The minimum rolling speed tungsten carbide rolls can be used at is one meter-per-second (1 m/s).
Proper cooling is crucial to ensure optimal performance of carbide rolls. The minimum recommended pressure is 4-to-6 bar and 250-to-300 liters per minute per passform.