Rotary Cutters Service & Support
Providing superior rotary cutting, slitting, and other cutting solutions is only part of the process. Hyperion Materials & Technologies also provides rotary cutter support services including technical engineering and design, manufacturing, after-sales support, maintenance, and carbide recycling services to customers with the goal of generating savings throughout the product life cycle.
Product Groups
Type: Rotary Cutter Engineering Design & Support
Location: on/off site
Description: Stand alone engineering service aimed at trouble shooting and/or optimization in order to enhance reliability or performance of rotary cutter solutions.
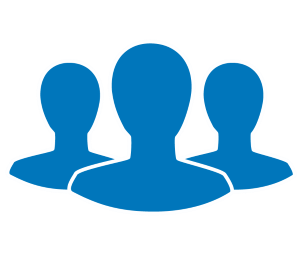
Type: Rotary Cutters After Sales Support
Location: on site
Description: Stand alone engineering service aimed at maximizing the performance of the rotary cutting solution provided by Hyperion Materials & Technologies.
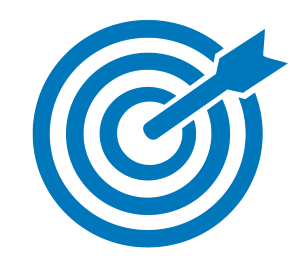
Type: Rotary Cutter Maintenance
Location: off site
Description: Re-sharpening and re-grinding capabilities allow our customers to maximize the life and performance of their rotary cutting dies and anvils. Hyperion Materials & Technologies also offers frame maintenance and repair services, along with servicing options for the entire rotary cutter.
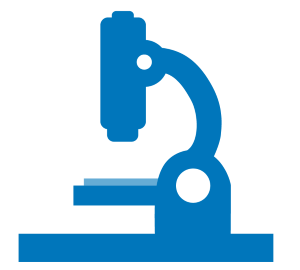
Type: Rotary Cutter Engineering Design & Support
Location: on/off site
Description: Stand alone engineering service aimed at trouble shooting and/or optimization in order to enhance reliability or performance of rotary cutter solutions.
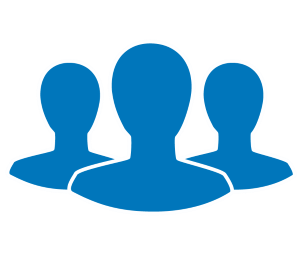
Type: Rotary Cutters After Sales Support
Location: on site
Description: Stand alone engineering service aimed at maximizing the performance of the rotary cutting solution provided by Hyperion Materials & Technologies.
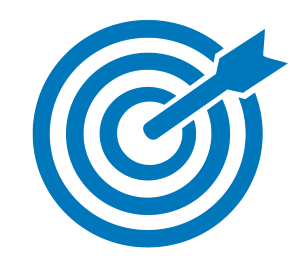
Type: Rotary Cutter Maintenance
Location: off site
Description: Re-sharpening and re-grinding capabilities allow our customers to maximize the life and performance of their rotary cutting dies and anvils. Hyperion Materials & Technologies also offers frame maintenance and repair services, along with servicing options for the entire rotary cutter.
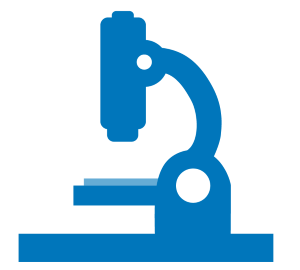
Engineering Design Support
Hyperion works with customers to provide a high level of engineering design and manufacturing support. Leveraging materials science and engineering expertise, Hyperion product specialists support customers with the selection of appropriate materials, the respect of tight geometric tolerances, and the design of user-friendly rotary cutting unit.
After Sales Support
Hyperion’s team of cutting solution experts provide unrivaled after sales support and engineering services to ensure cutting units are properly installed and functioning with the converting process. This can include start up assistance, advanced training, on-site audits and technical support for solutions, manuals, and more.
Maintenance
Hyperion provides mainteance and re-sharpening services for rotary cutters and other cutter solutions at its maintenance centers in Europe, Asia, and the Americas. Stringent quality standards ensure consistent quality for customers, regardless of where they may be located or which Hyperion maintenance center they utilize.
Recycling
Hyperion can partner with customers to recycle most carbide materials. In addition to the environmental benefits, customers can reduce their obsolete stocks while at the same time create a source of income.
Frequently Asked Questions about Rottary Cutter Services
Hyperion Materials & Technologies offers regrinding and resharpening services and frame maintenance for rotary cutter modules, rotary dies, and anvils at its dedicated maintenance centers in Epinouze, France in Europe; West Branch, Michigan, USA in North America; Diadema, Brazil in South America; and Pune, India and Wuxi, China in Asia. Hyperion’s stringent quality standards ensure consistent quality for our customers, regardless of where they may be located or which Hyperion re-sharpening center they utilize.
Hyperion’s sharpening precision and consistency guarantee the best possible results between resharpening. In addition, our tight tolerances ensure the strictest minimum diameter reduction for both cutters and anvils, which leaves more material for future sharpening, maximizing the total lifetime of the tools.
Door-to-door lead time for resharpening and regrinding services by Hyperion can vary depending on a variety of factors, including the condition of the tooling and extent of services required. Most maintenance service provided by Hyperion Materials & Technologies can be performed with a door-to-door lead time as fast as two weeks.
Hyperion supports customers with technical problems by dispatching a local representative to the site with the problem to collect information on the problem. A Hyperion rotary cutter engineer will use the information to support the customer remotely.
If the engineer is unable to solve the problem remotely, an on-site visit will be scheduled for the engineer to assist at your facility.
Hyperion Materials & Technologies can support the engineering and design of cutting tools for rotative cut, straight cut, and slitting applications.
Hyperion’s team of experienced engineers partner with customers to develop cutting tools and solutions that are specifically tailored to their unique needs. In addition, Hyperion offers a full range of support services including:
- Research and Development support for tungsten carbide
- Technical consultation and design assistance
- Material selection and prototyping
- Airflow analysis
- Vibration analysis and modeling
- After-sales support and maintenance
- Manufacturing and implementation support
- Start-up assistance
- Operator and maintenance training
- On-site technical troubleshooting and support
- On-site audits of cutting solutions
- User manuals
Maintenance support including anvil regrinding, rotary die resharpening, frame maintenance, and more.
Hyperion Materials & Technologies, through its Carbide Recycling Program, purchases used carbide rotary cutter tools and products from its customers to convert them back into usable raw materials for future production. Using a controlled, certified chemical recycling process, Hyperion ensures these “new” materials are identical to materials produced from mined ore.